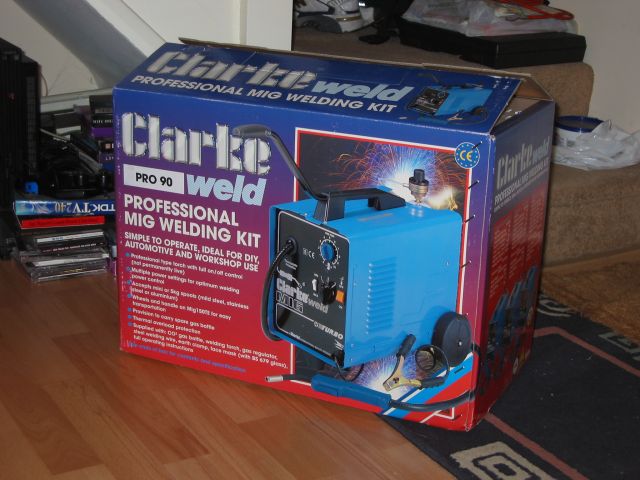
So just one day at the shed this weekend. The new shields were over the head rather than hand held. They do look rather sinister though.
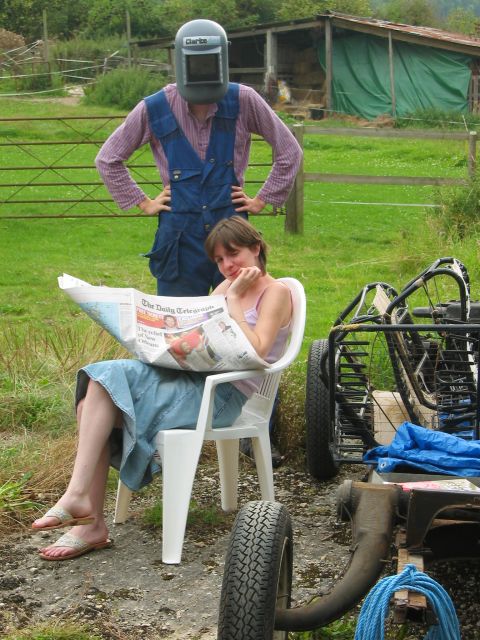
The welder came with C02 gas and as we discovered last time around we needed a C02/Argon mix because we're welding such thin metal. I'd got some mix as well but we had some trouble fitting the regulator to the bottle (one of the disposable ones). We got there in the end but the calibration is all wrong.
That problem aside everything worked fine. Using the mix rather than straight CO2 made a huge difference and we were getting much cleaner welds, much less spitting and it was easier to get a pool going without blowing through the body. We spent some time playing with the new welder on some practice metal to get a feel for the voltage and wire speed settings, and Sarah took the chance to have her first go at welding.
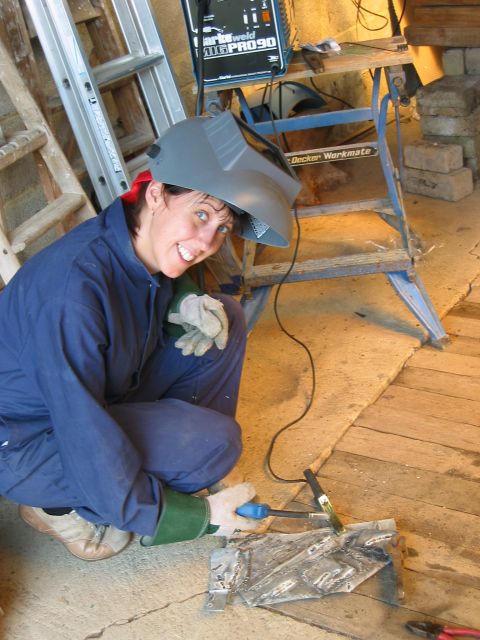
Ross finished up shaping a patch to go under the car, under the drivers feet. It was a complex piece matching the channels in the body. The last weekend we'd fashioned a tool just for this job by welding a bar of the right diameter to the top of a larger t-bar. With this clamped in a vice it was perfect for bashing against.
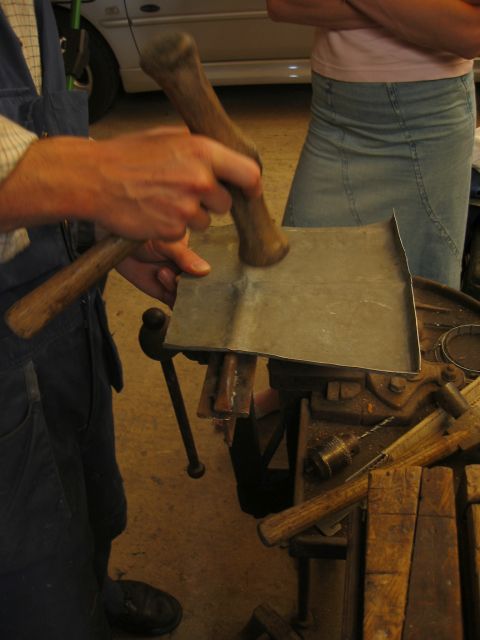
Unfortunately the patch was too thin, or possibly not steel. When Ross tried to weld it on the mig really fizzed when the contact got near the patch and the patch metal was just blown away. This will be a bit of a set back as we're not sure we've got any more metal of the right thickness. We pressed on though - and tried the one furtherest back under the body. This was really awkward being upside down but I think we still got a better weld on it that we had with any of our CO2 attempts.
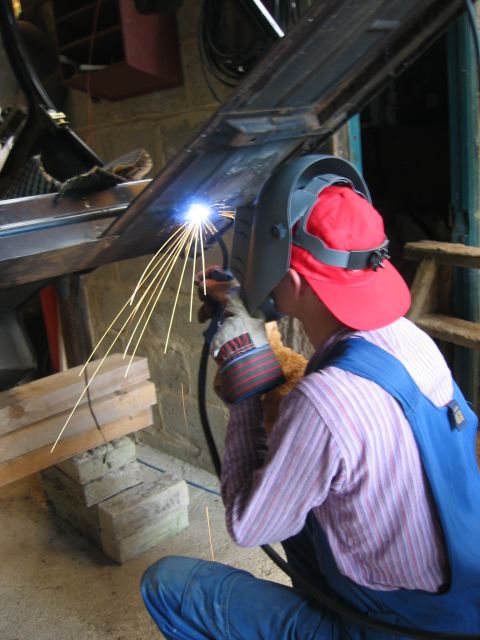
While I was under the car welding, Ross and Sarah were grinding down a patch inside the car so that our new footwall patches will fit snugly.
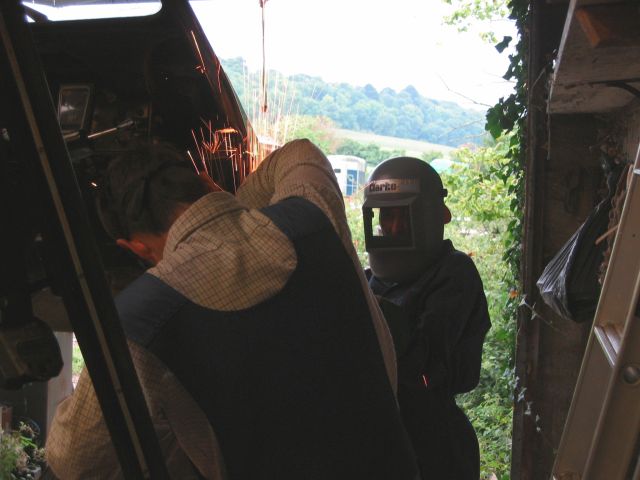
After doing the last patch we had left on the underside we lowered the car back down so it was more level and got to welding in the passenger side footwell patch. It distorted a bit under clamping but we got one side of it welded (missing out the channels in the underlying body for now). The weld was a lot cleaner than any we've had so far, and Ross recons it was better than some of the existing body patchwork ;)
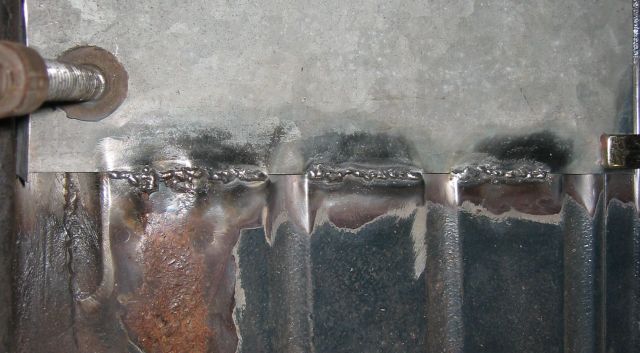